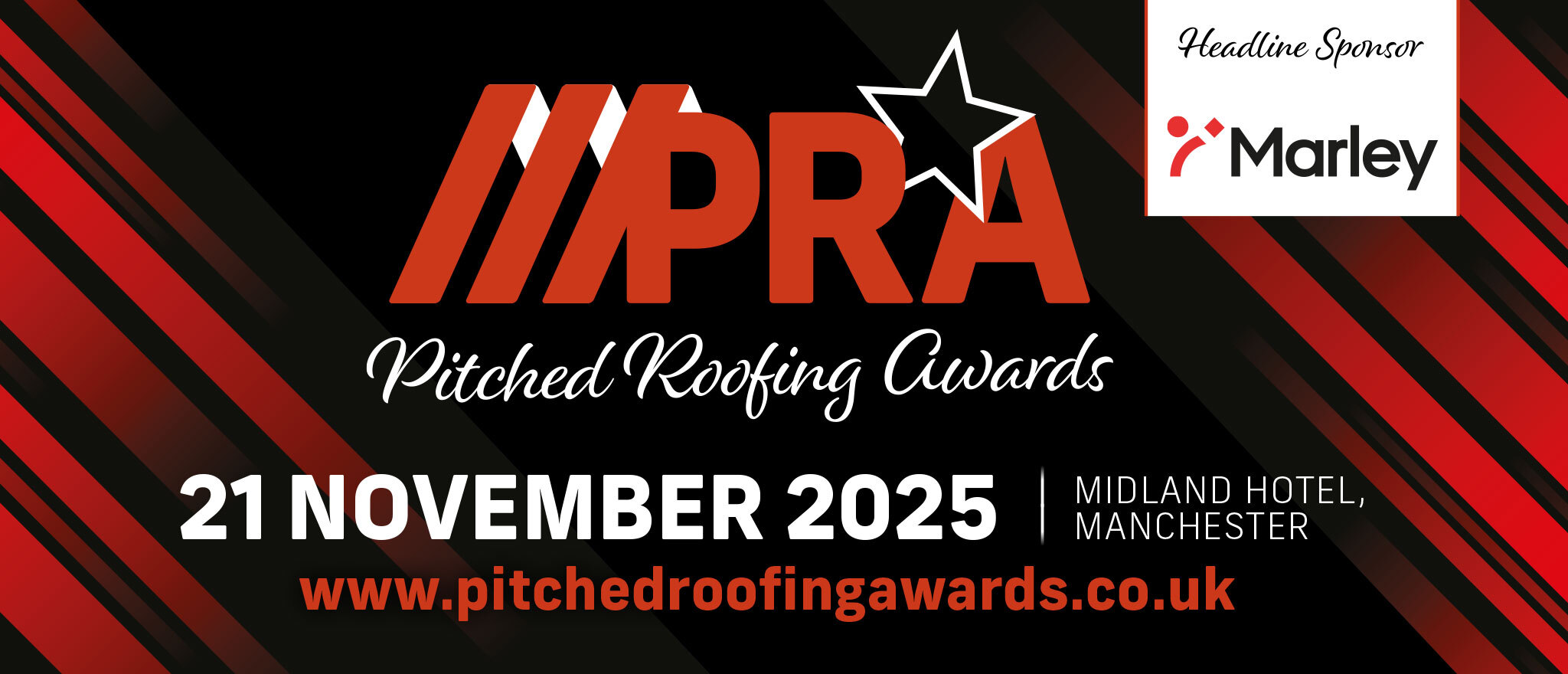
WELCOME
The 2025 Pitched Roofing Awards are back! Join us on Friday 21 November, as we recognise the most outstanding projects and innovations in the industry.
Entries are now open! Showcase your expertise and don't miss our brand-new Integrated Solar Systems category.
Submit your entry today and be part of the industry's biggest celebration.
Joe Ayling
Editor
RCI Magazine